Global Environment
We contribute to the realization of a recycling-oriented, low-carbon society through measures to combat climate change and reduce food loss.
Climate Change Countermeasures
Introductory video: “TRY SDGs: NIPPON ACCESS’s Climate Change Countermeasures” (3 min. 57 sec.)
Conversion to LED Lighting and Introduction of Solar Power Generation Systems
We have almost completed the conversion of all lighting equipment to LEDs at our distribution centers and are currently upgrading to next-generation LEDs. As of April 2023, we have installed solar power generation systems at 22 sites, resulting in a reduction of over 3,000 tons of CO2 emissions.
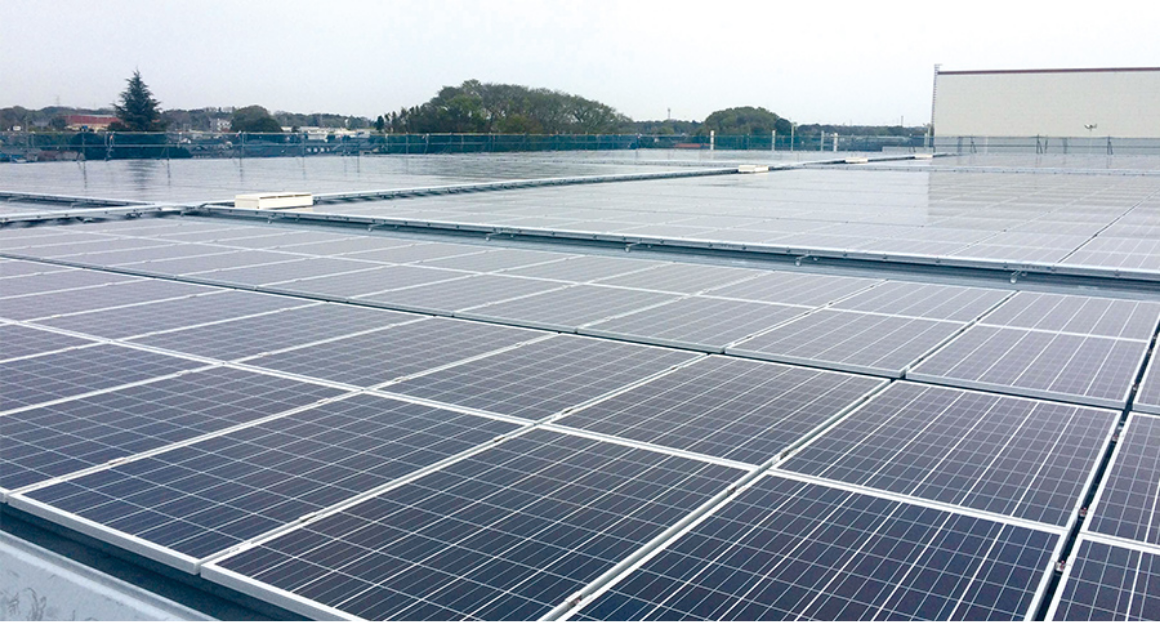
Conversion to Hybrid Vehicles and Telematic Systems
We have introduced hybrid vehicles for some of the company cars used at our bases nationwide. We are also gradually expanding the use of telematics systems to curb idling and sudden starts, which not only prevents accidents but also reduces CO2 emissions. The introduction of hybrid vehicles has reduced CO2 emissions by approximately 58 tons per year.
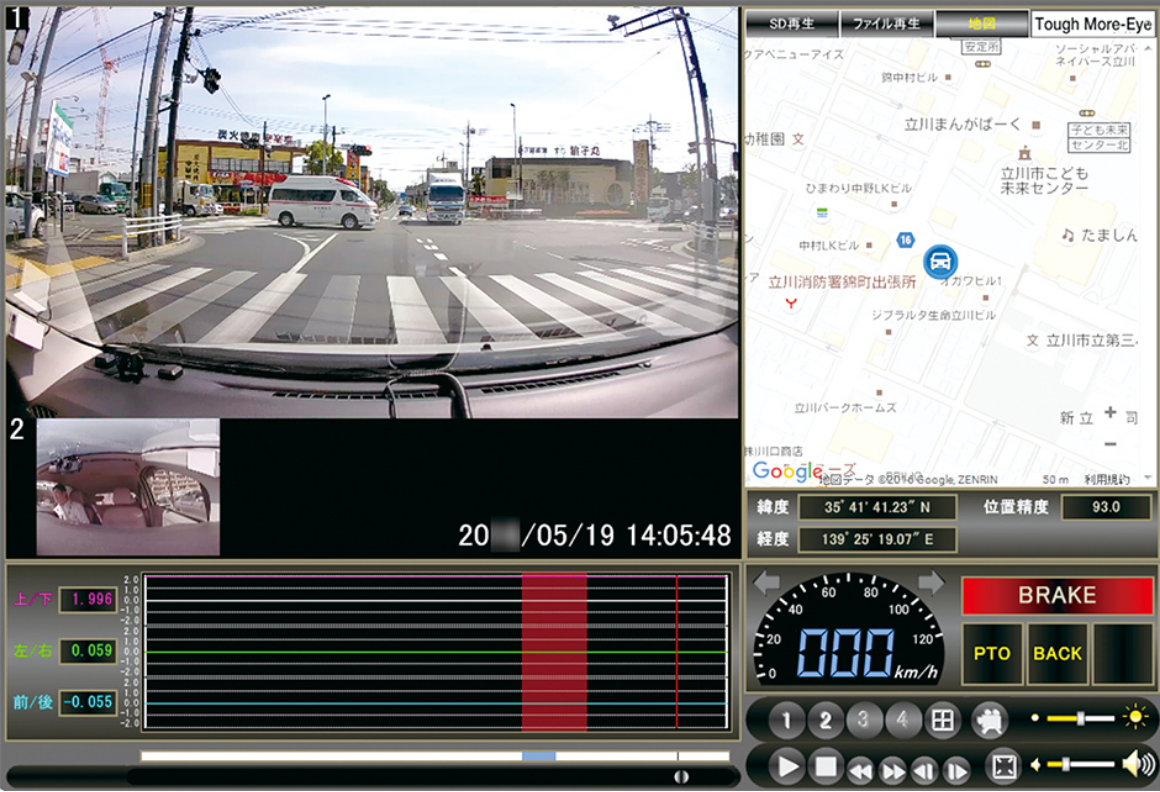
Driving image with telematics
Energy Reduction through Thermal Barrier Coating of Centers
Thermal barrier coating reduces the rise in temperature inside distribution centers in summer, lowering the indoor temperature by 5°C to 10°C and reducing the energy used for air conditioning equipment. As of April 2023, we have applied heat shield coating at 27 of our centers.

Difference in temperature with thermal barrier coating (the coated surface is about 10°C)
Five Year Energy Transition at All Sites
Our energy consumption is primarily electricity, and both our usage and energy consumption per unit are on a decreasing trend. Although overall energy consumption increased due to business expansion in FY2018 and FY2019, energy consumption per unit has continued to drop.
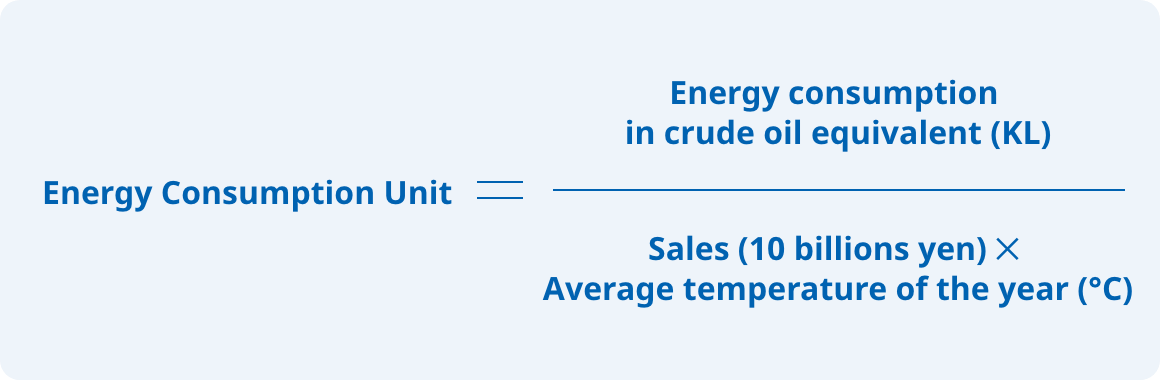
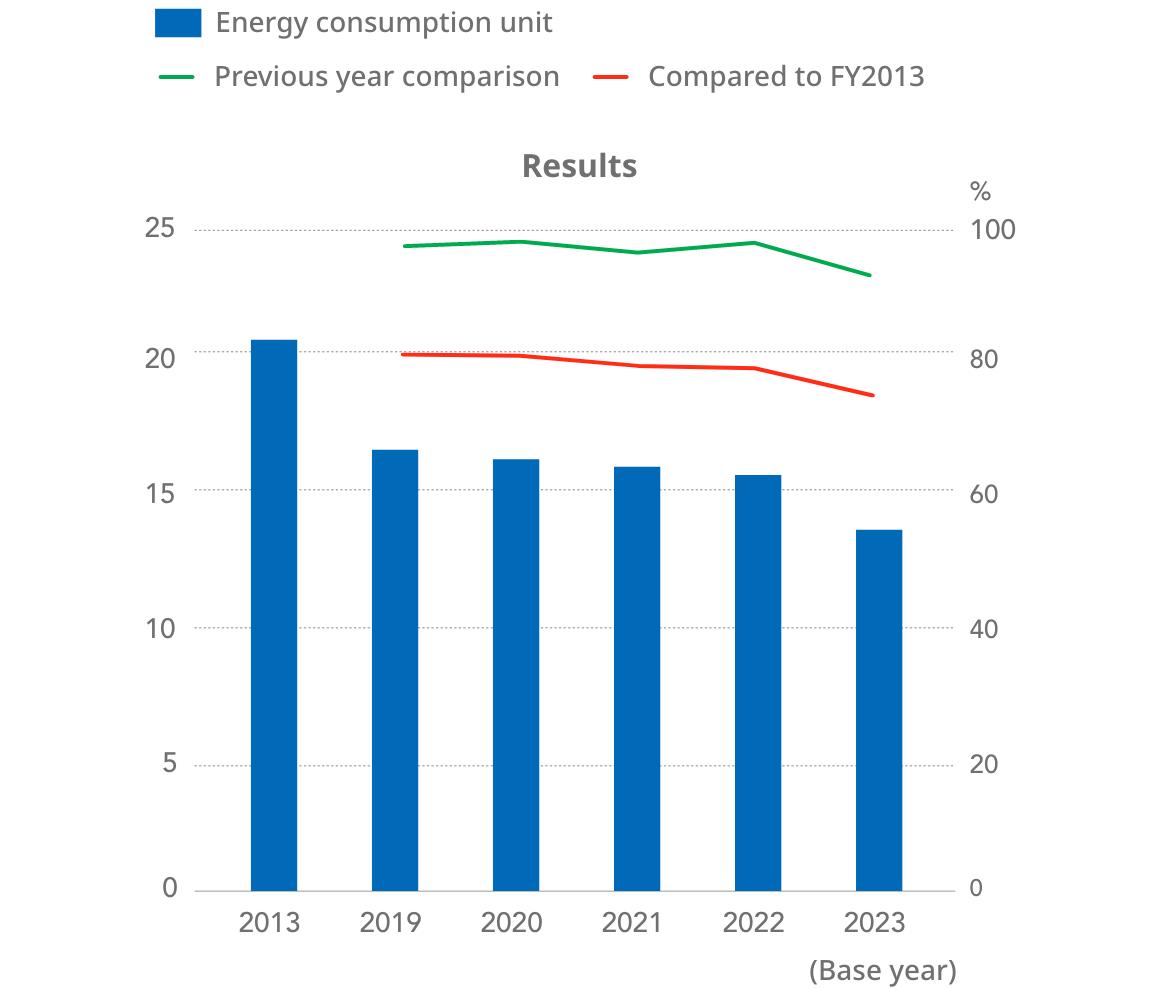
Recipient of S-Rank for Energy Conservation for Eighth Consecutive Year
Based on the Energy Conservation Act Periodic Report, our company has achieved the highest S-rank for eight consecutive years from FY2015 to FY2022 in the classification evaluation system for businesses.
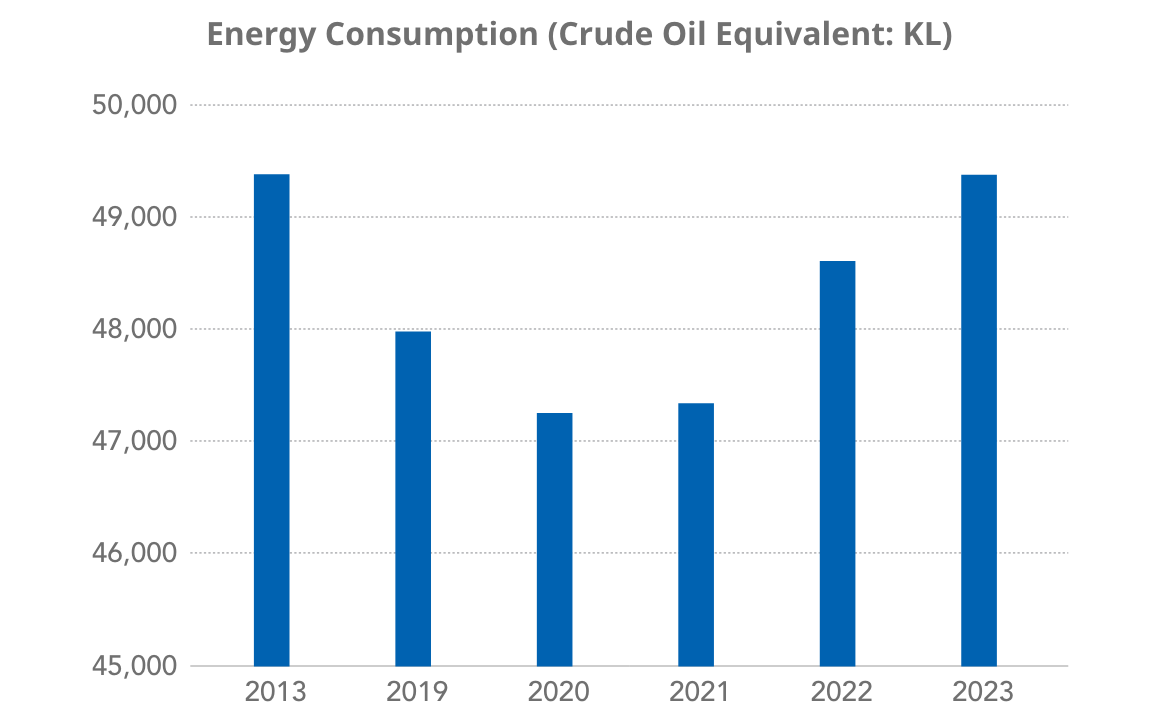
Promotion of Logistics Rationalization and Streamlining (Introduction of Standardized Crates)
Upon conducting an analysis of work hours, it was found that deliveries were being delayed due to crate organizing and transportation to the sales floor. By introducing standardized crates, we were able to reduce the burden of organizing tasks for drivers both at stores and distribution centers.
*We are proud to announce that our company was awarded the Excellence Award at the 2022 Supply Chain Innovation Awards hosted by the Ministry of Economy, Trade and Industry for the above efforts in collaboration with Tokyu Store Co., Ltd.
*It was our second consecutive year to receive this award.
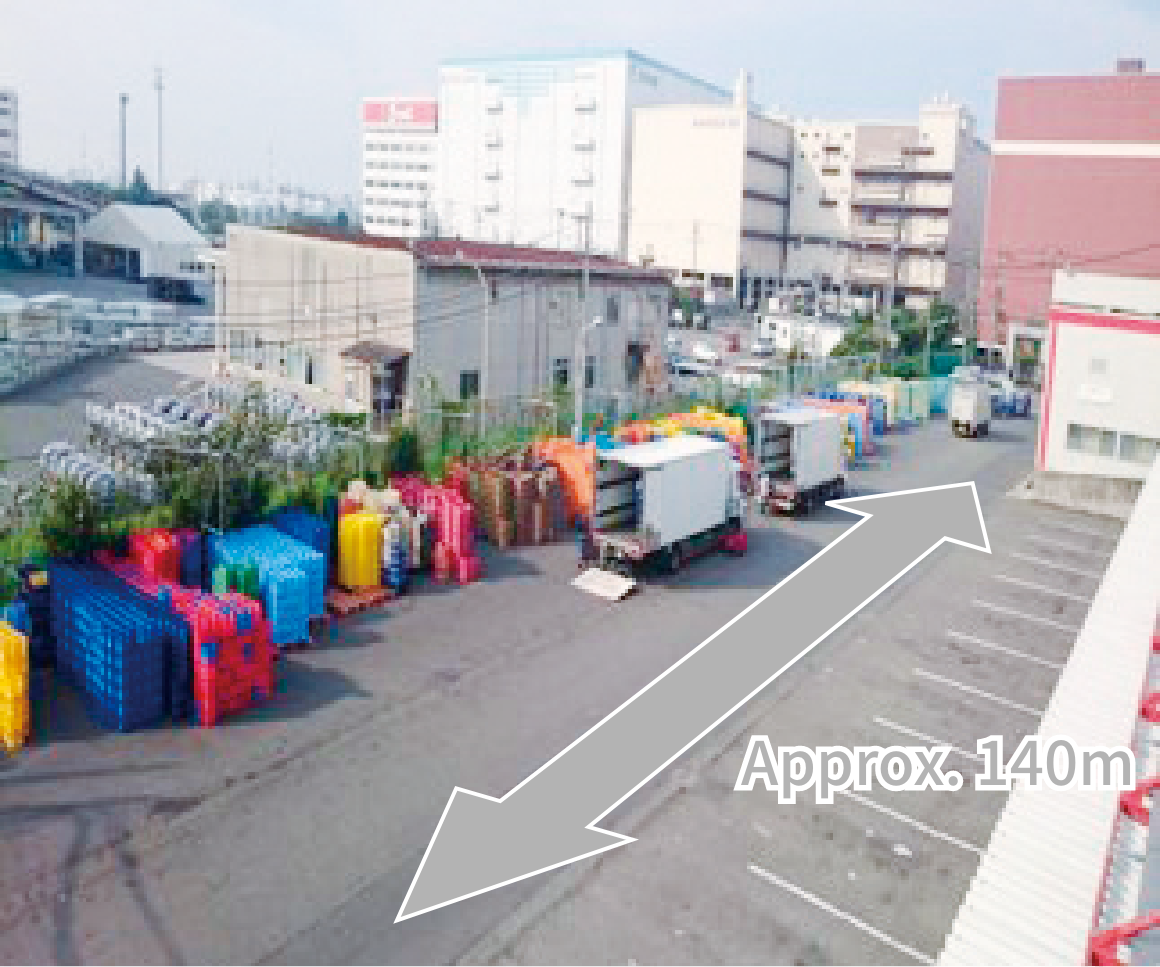
(Before) Approx. 120 types of crates
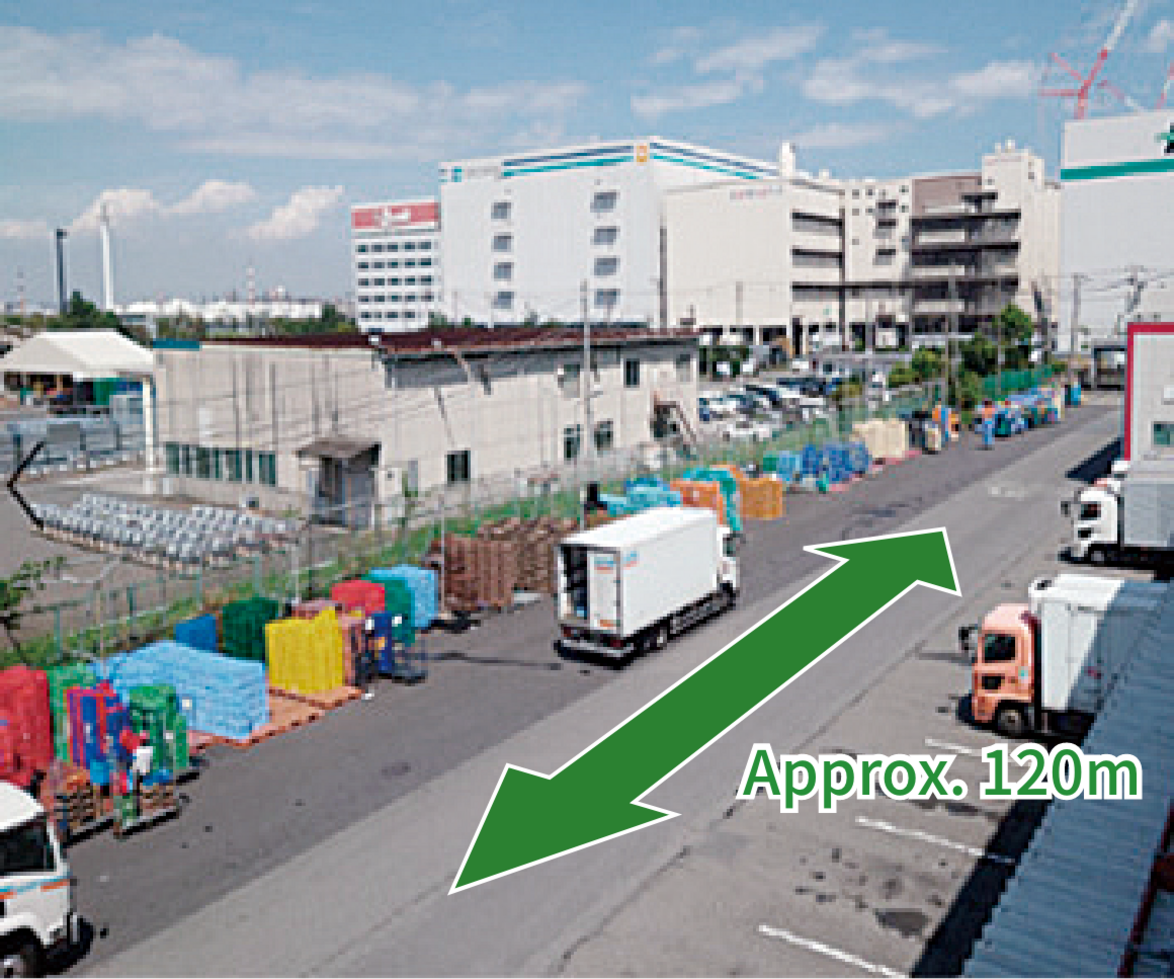
(After) Approx. 60 types of crates *Approx. 60 types were replaced by standardized crates
Optimization of Delivery Routes
We are actively promoting digital transformation (DX) through the use of delivery simulators, TMS, BI tools, and dynamic management terminals to improve loading rates, optimize delivery routes, and reduce the number of vehicles. By limiting the distance traveled, fuel consumption and CO2 emissions are also reduced.
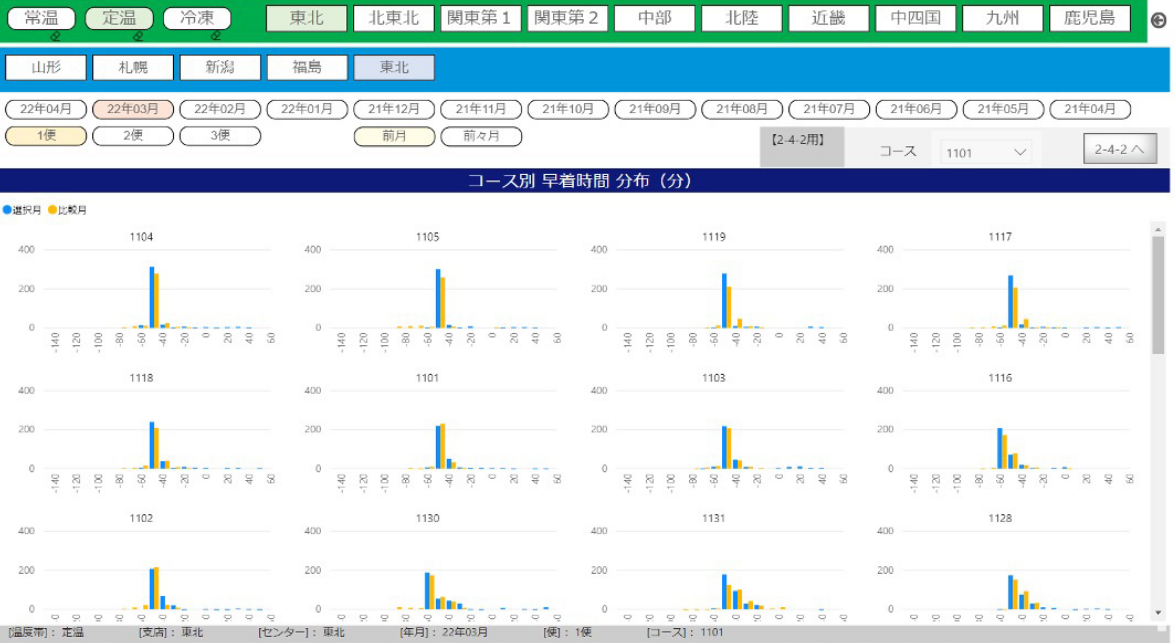
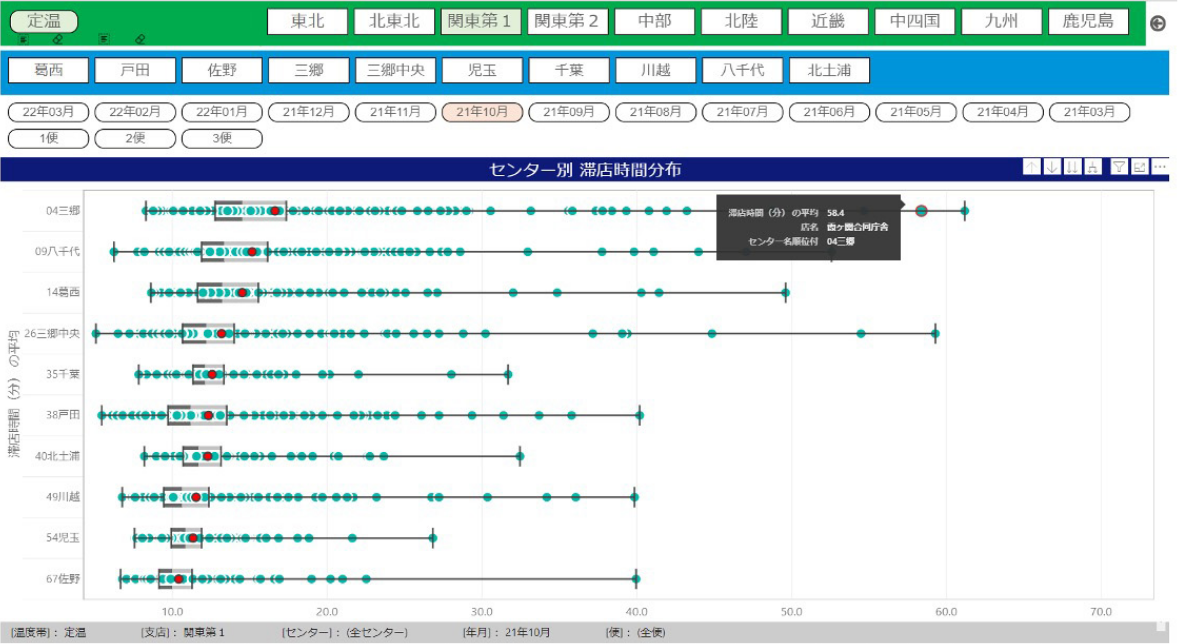
BI tools to visualize delivery KPIs and identify potential points for improvement
Reducing Food Loss and Waste
Four phases to control food loss

Introductory video: “TRY SDGs: NIPPON ACCESS’s Food Loss Countermeasures” (3 min.)
PHASE 1
Prevent loss
Not causing loss to begin with is the most important. This can be achieved through product development measures such as improving demand forecasting accuracy, ensuring precise ordering and management, and incorporating products with longer expiration dates and packaging materials suitable for extended storage.
■Appropriate Order Management
Continuous improvement using IS014001 (case study of the Logistics Control Department of the Sales Division)
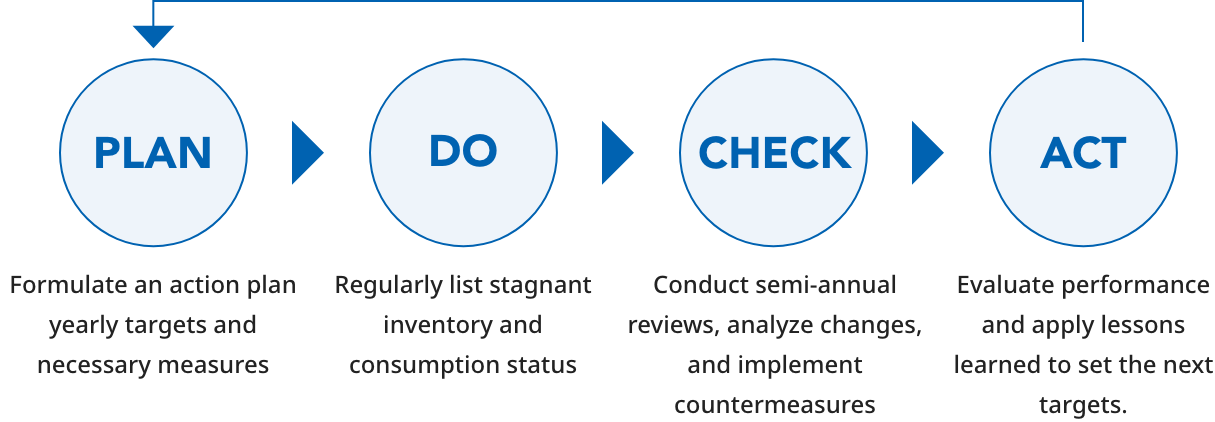
PHASE 2
Sell out
In the event of stagnant inventory or overdue deliveries, we consider how we can leverage our various channels to sell everything.
■Utilizing Our E-commerce Store, Smile Spoon
-Selling Directly to Consumers through Amazon, Rakuten, Yahoo! -
Comprehensive online and offline efforts for private brand products ⇒ Increasing brand power and added value by explaining the quality of products and conveying the producers’ ethos ⇒ Increased sales + reduced food loss
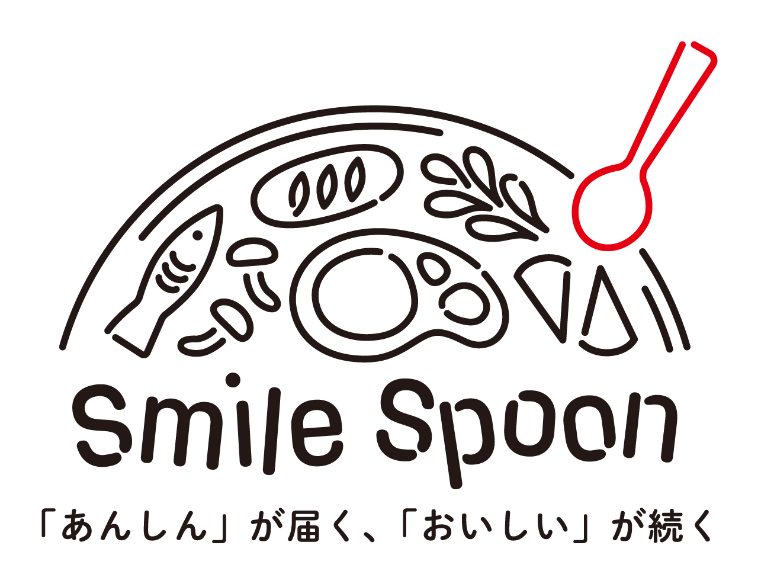
PHASE 3
Distribute
When we can no longer expect to sell certain products, we donate them to food banks or distribute them internally to reduce waste as much as possible.
■Increasing food bank donations
We are increasing our donations to food banks across the country. We began donating in FY2021, and as of March 2023, we have donated to 23 locations and 18 food banks.
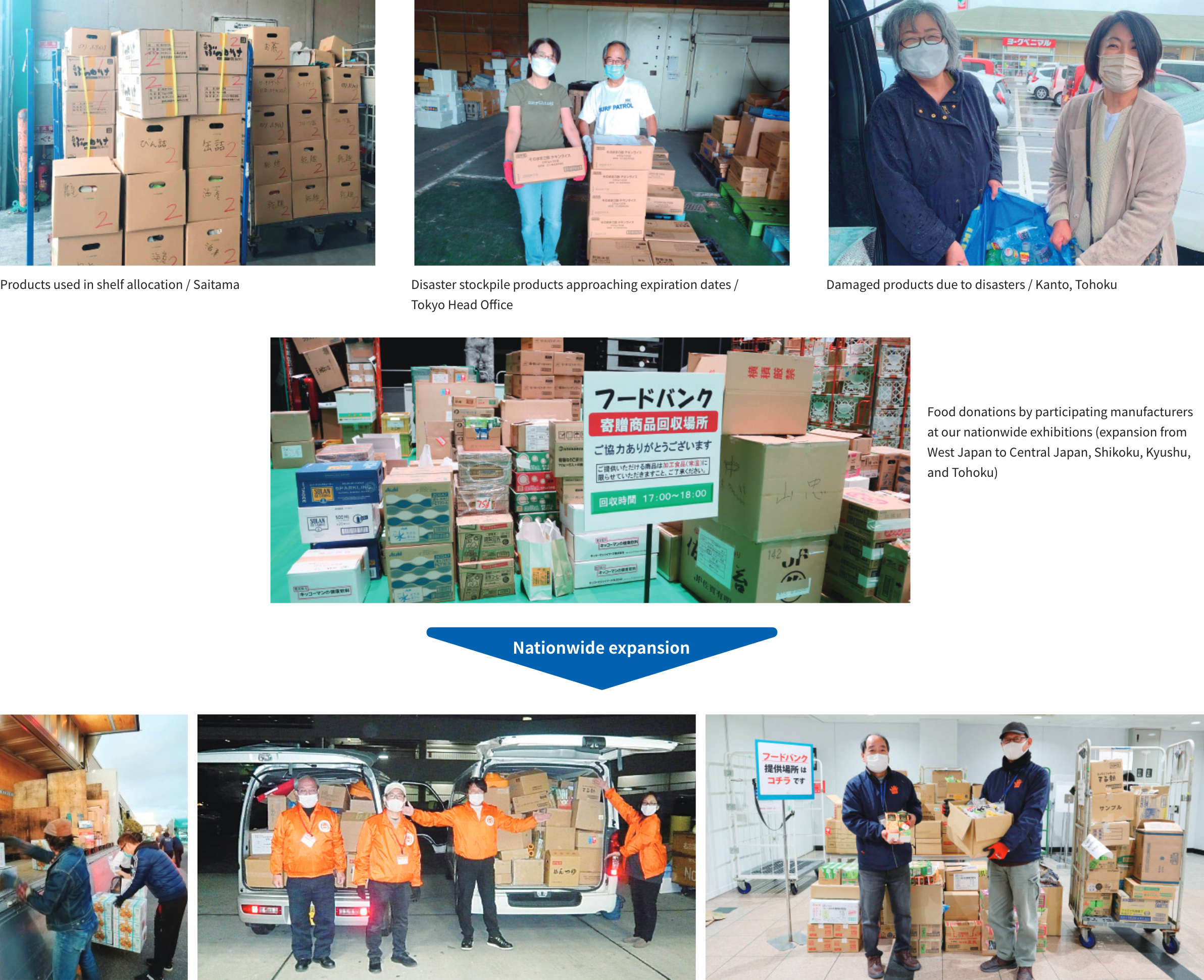
PHASE 4
Recycle
If we must dispose of products, we recycle as much as possible. We search for recycling companies in the area, and make sure to visit them and confirm that they are reliable before making use of their services.
■Promotion of Food Recycling
We prioritize outsourcing food waste to recycling processors for purposes such as feed and fertilizer production. Since FY2013, we have achieved a recycling rate of 70% or higher annually and are striving for further improvement.
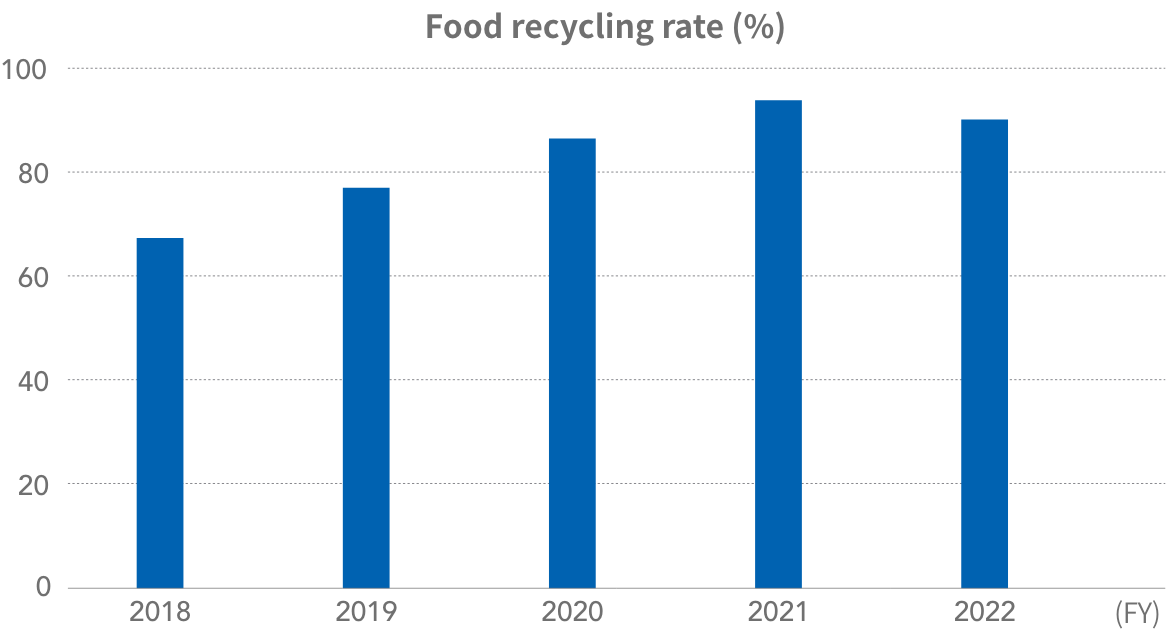
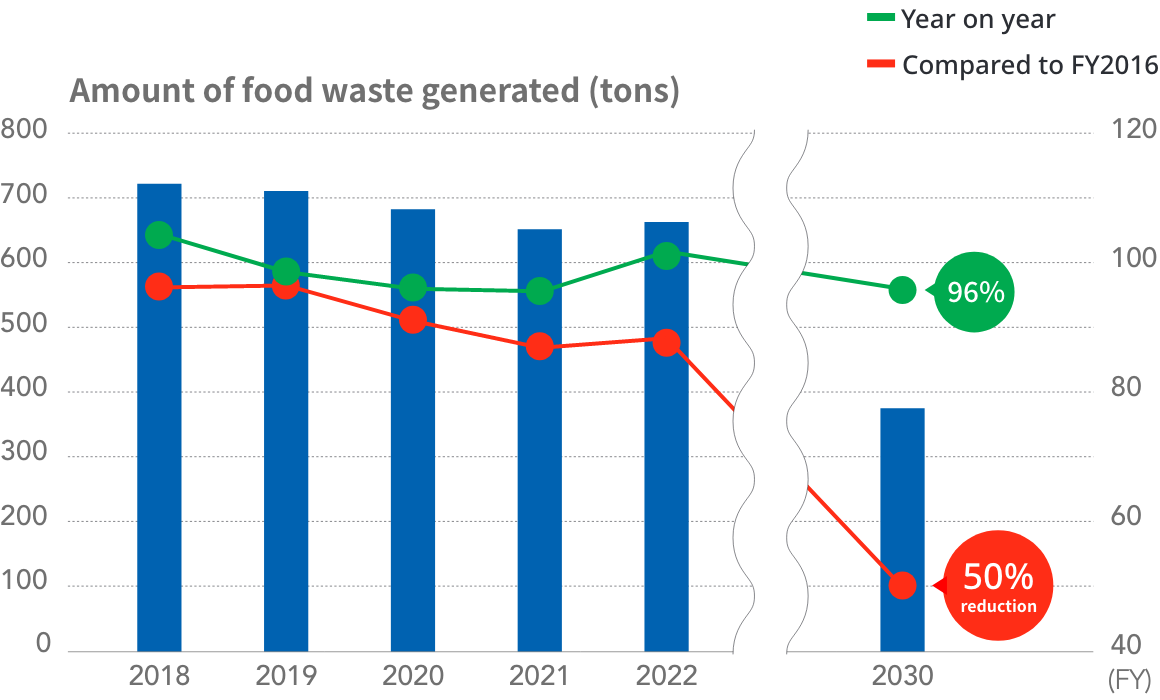
Winner of Food Loss Reduction Award from the Consumer Affairs Agency, and Consumer and Food Safety Award from the Cabinet Office’s Minister of State for Special Missions.
Our food loss reduction initiatives were recognized by the Consumer Affairs Agency’s Food Loss Reduction Awards, with the Cabinet Office’s Minister of Special Missions Consumer and Food Safety Award.
*Click here for more details
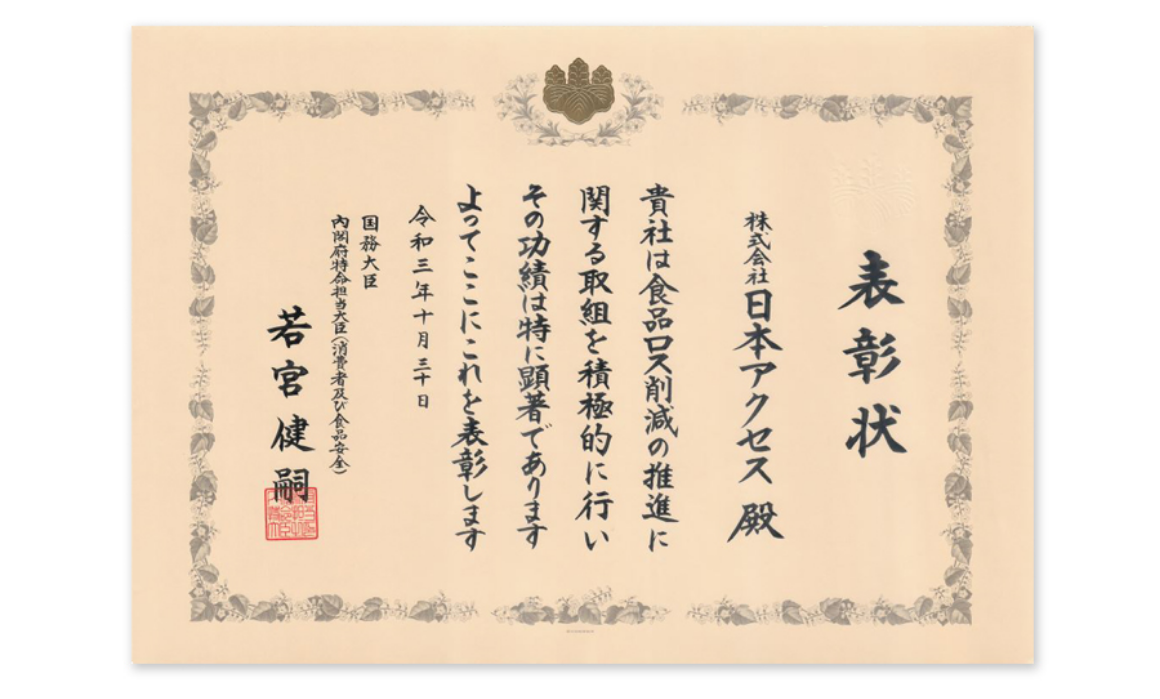
Awarded the Minister of Agriculture, Forestry and Fisheries Award at the 10th Food Industry Waste Reduction Awards sponsored by the Ministry of Agriculture, Forestry and Fisheries
In January 2023, our efforts to reduce food loss by connecting manufacturing, distribution, and sales were recognized, and we were awarded the Minister of Agriculture, Forestry and Fisheries Award, the top prize at the Food Industry Waste Reduction Awards.
*Click here for more details
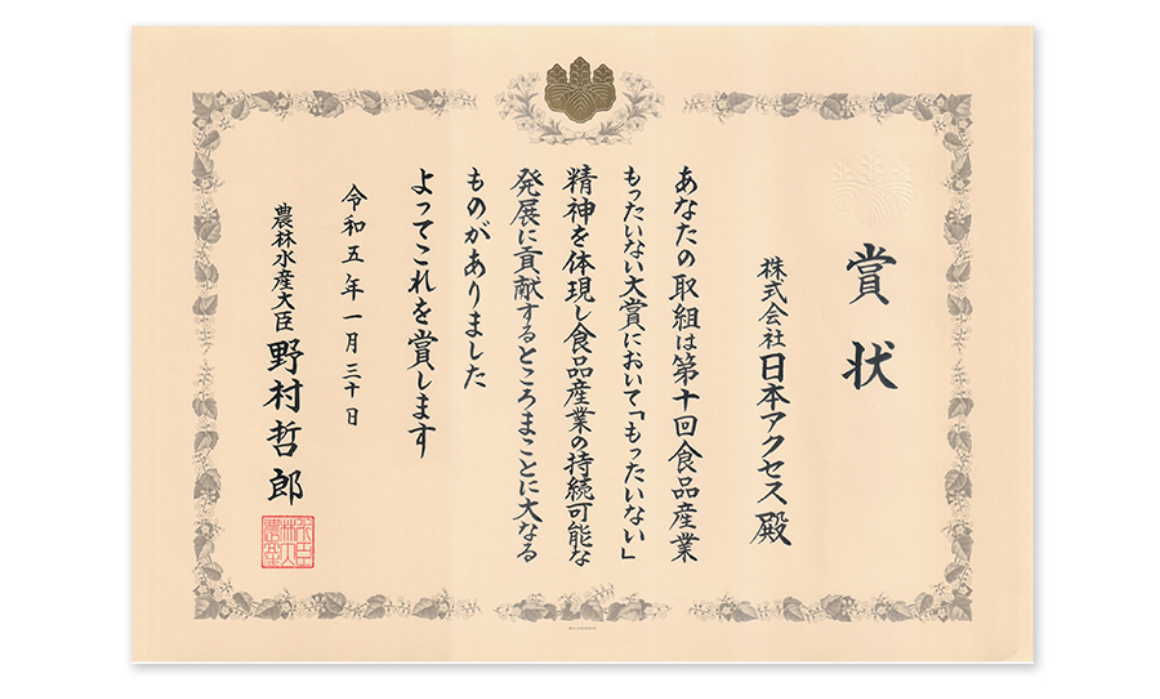
ISO14001 Certification
In 1999, our partner company Nishino Shoji obtained ISO14001 certification, and we have continued to renew this certification since our merger with them in 2007.
Scope: Product purchasing, sales, storage, distribution processing, delivery, product development, office operations, etc. in the food wholesale business at the head office
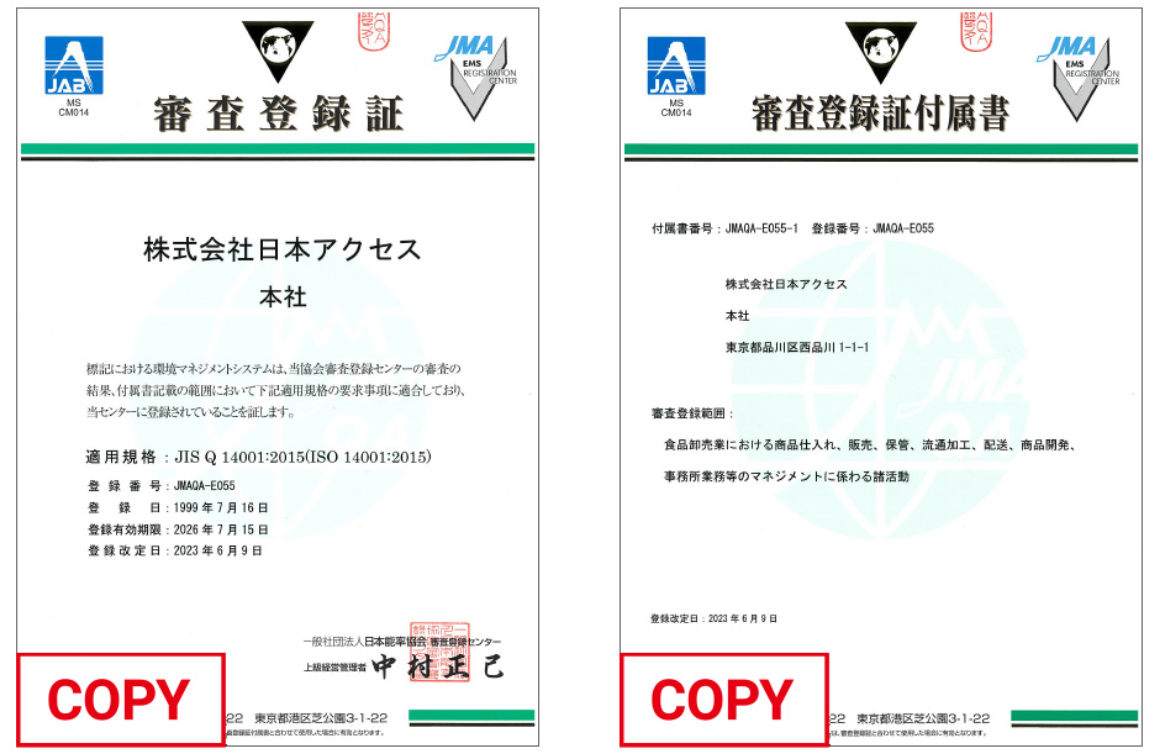